Eine neuartige, kompakte Dosier-Misch-Einheit ist das Herzstück der von Fette Compacting entwickelten Anlage zum Continuous Manufacturing. Dieses Verfahren setzt sich in der Produktion von Arznei- und Nahrungsergänzungsmitteln immer stärker durch. Die Prozesseinheit FE CPS führt bei der Tablettierung verschiedenste Ausgangsmaterialien auf präzise Weise in einen kontinuierlichen Fluss. Beim Design der Anlage gingen die Entwickler an vielen Stellen neue Wege.
Für Hersteller gibt es eine ganze Reihe an Gründen, auf Continuous Manufacturing zu setzen. Vor allem ist die kontinuierliche Direktverpressung durch integrierte Prozesse im Vergleich zum Batch-to-Batch-Verfahren wesentlich effizienter und prozesssicherer. Zudem sorgen das schlanke, platzsparende Design und die einfache Bedienung für signifikant niedrigere Investitions- und Betriebskosten. Darüber hinaus ermöglicht das Verfahren verkürzte Vorlaufzeiten, flexible Chargengrößen und eine Echtzeit-Inprozesskontrolle. Insgesamt steigt die Produktqualität, wobei oftmals auch kürzere Markteinführungszeiten für neue Produkte möglich sind.
Hinter diesen Vorzügen stehen eine Vielzahl von Konstruktionsentscheidungen sowie ein ausgeklügeltes Zusammenspiel von Technologien und Prozessen.
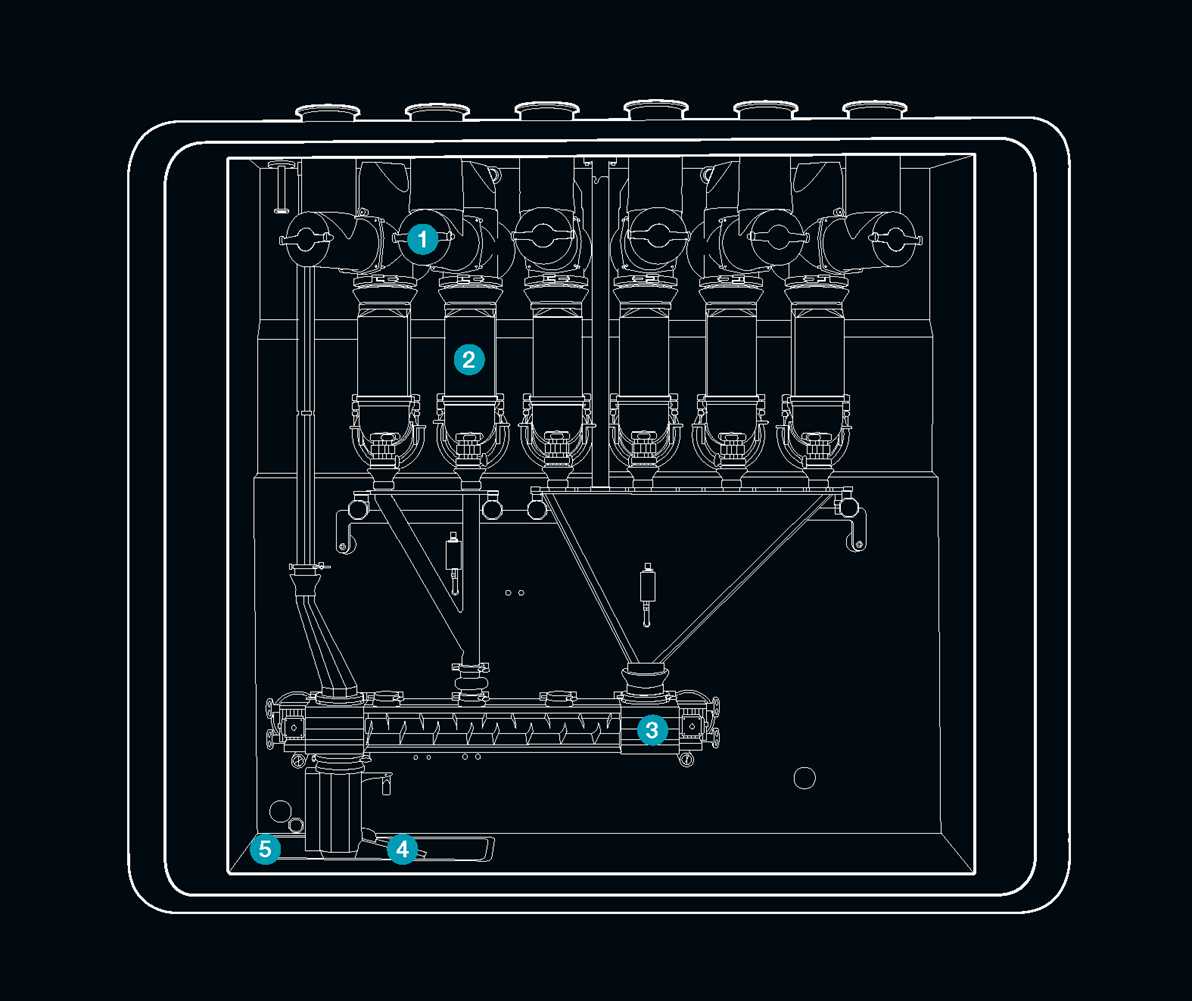
Bild: Fette Compacting
Ein neuer Weg zu einem vielseitigen Design
Eine entscheidende Rolle auf dem Entwicklungsweg für die kontinuierliche Direktverpressung spielte der Quality-by-Design-Ansatz. Mit diesem Weg konnte Fette Compacting verschiedenste material- und prozessbezogene Szenarien erproben – und dadurch ein vielseitiges Design erreichen. Aus diesem Vorgehen resultierte letztlich die Dosier-Misch-Einheit mit der Bezeichnung „FE CPS“, mit der sich bis zu sechs unterschiedliche pulverförmige Ausgangsmaterialien genau dosieren, mischen und an den nachgelagerten Tablettierprozess übergeben lassen. Im Zusammenspiel mit einer Rundläufertablettenpresse und einem zentralen Bedienterminal entsteht eine vollständige kontinuierliche Direktverpressungslinie, die auf nur einer Ebene in bestehende Produktionsräume integrierbar ist. Damit lassen sich Inhaltsstoffe in einem variablen Durchsatzbereich von fünf bis 200 Kilogramm pro Stunde verarbeiten.
Ein Blick auf die einzelnen Prozessschritte zeigt, was die Technologie der Dosier-Misch-Einheit im Besonderen auszeichnet.
Störungsfrei zuführen und dosieren
Die Zufuhr legt bei der kontinuierlichen Tablettenproduktion den Grundstein für den korrekten Betrieb der gesamten Anlage. Hierbei sind vor allem Pulver mit einer besonderen Beschaffenheit hinsichtlich Dichte, Fließfähigkeit, Kohäsion oder Adhäsion bei der Nachfüllung anfällig für Pulverphänomene wie Anhaftungen oder Brückenbildungen. Damit selbst solche anspruchsvollen Rohmaterialien zuverlässig und gleichmäßig in den Dosierprozess gelangen, hat Fette Compacting bei der FE CPS die Öffnungen für die Materialzufuhr von einzelnen Zutaten oder Vormischungen mit einem automatischen Nachfüllsystem (Automatic Refill System, ARS) ausgestattet. Die automatische Dosierung übernehmen bis zu sechs gravimetrische (Loss-in-Weight, LiW) Pulverdosierer, die die erforderliche Fördermenge durch Kombination der hinterlegten Konzentration des Materials mit dem geforderten Anlagendurchsatz errechnen. Doppelschnecken sorgen zudem für eine Dosierung des Materials in den nächsten Prozessschritt mit minimaler Zufuhrvariabilität.
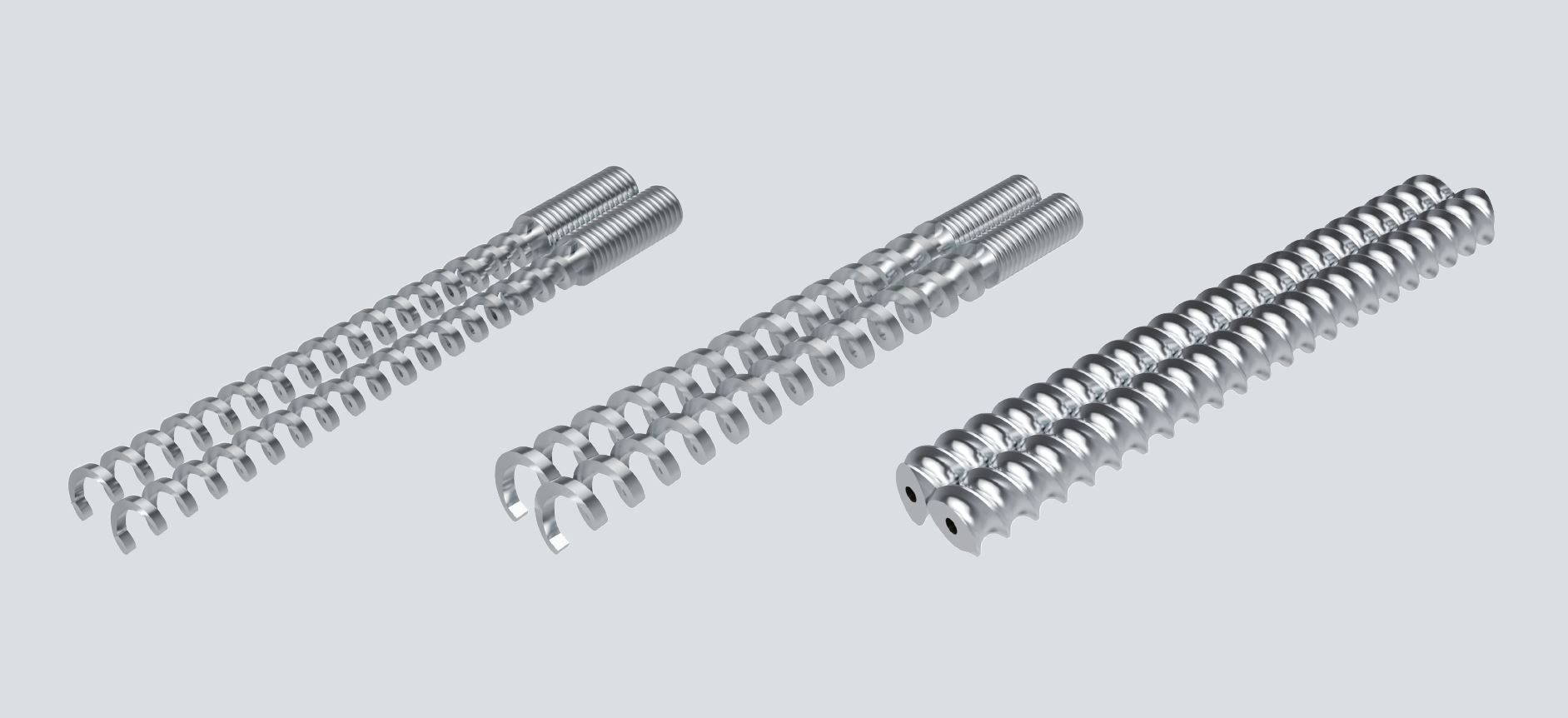
Bild: Fette Compacting
Entkoppelte Mischzonen
Im Unterschied zu konventionellen horizontalen Mischern setzt das Anlagendesign auf zwei aufeinanderfolgende, aber entkoppelte Mischzonen. Dadurch entfällt die tote Zone im Zwischenbereich, wobei pro Mischzone zwei Einlassöffnungen mit einer Kombination von Fallrohren und Übergabetrichtern zur Verfügung stehen. Dadurch lassen sich Mischprozesse sowohl mit hoher als auch mit niedriger Scherenergie in einem einzigen Mischer kombinieren. Das sorgt für optimale Mischergebnisse für die jeweiligen Rezepturanforderungen. Die spezifische Trichterkombination und verschiedene Trichterkonfigurationen ermöglichen eine große Flexibilität. So lässt sich für jeden Inhaltsstoff die individuelle Mischzeit bestimmen und die bestmögliche Prozesseinstellung für ein breites Spektrum an Rezepturen erreichen.
Mit ePAT zur integrierten Prozessanalyse
Am Ausgang des Mischers ist zudem eine eingebettete Prozessanalytik (embedded Process Analytical Technology, ePAT) einsetzbar, die zur kontinuierlichen Prozessanalyse einen neuen Ansatz verfolgt: Die Sensorik ist vollständig in die Anlage und deren Steuerung integriert. Das senkt den Einrichtungs- und Betriebsaufwand zusätzlich. ePAT nutzt hochentwickelte in die Prozesseinheiten eingebaute Sensoren. Sie überwachen permanent die wichtigsten Qualitätsmerkmale. Durch die Messung im Produktfluss ist eine unmittelbare Kontrolle des Produktionsprozesses möglich. Die Sensorspektrometer sind direkt mit dem Controller der Maschine verbunden. Über Sensoren für die Nahinfrarotspektroskopie (NIRS) wird die Produktqualität auf Basis von chemischen und auch physikalischen Eigenschaften in Echtzeit überwacht.
Die NIRS erfasst im Spektralbereich von 750 bis 2.200 Nanometern durch ein tiefes und zugleich beschädigungsfreies Eindringen der Strahlen die meisten Wirkstoffe. So steht ein cGMP-konformes Werkzeug mit ultrakurzen Messzeiten zur Verfügung, das selbst bei den großen Probenmengen einer kontinuierlichen Direktverpressung reibungslos funktioniert. Es hat es sich als besonders robust erwiesen und der Ein- und Ausbau erfolgen werkzeugfrei. Die zentrale Steuerung übernimmt das Human-Machine-Interface der Tablettenpresse.
Die Sensoren lassen sich an verschiedenen Messpunkten einsetzen: am Auslass des Mischers, am Einlass der Tablettenpresse oder der Fill-O-Matic. Hierbei lässt sich am Tablettenauswurf die Wirkstoffkonzentration der Tabletten zu 100 Prozent erfassen und eine Aussortierung einzelner Tabletten durchführen. In Entwicklungsphasen würden in der Regel mehrere Messpunkte der Anlage bestückt, um möglichst viele Daten erfassen und alles über die Prozesse zu erfahren. Im Rahmen einer aktiven Produktion kämen hingegen ein bis zwei Messpunkte für die Qualitätskontrolle zum Einsatz.
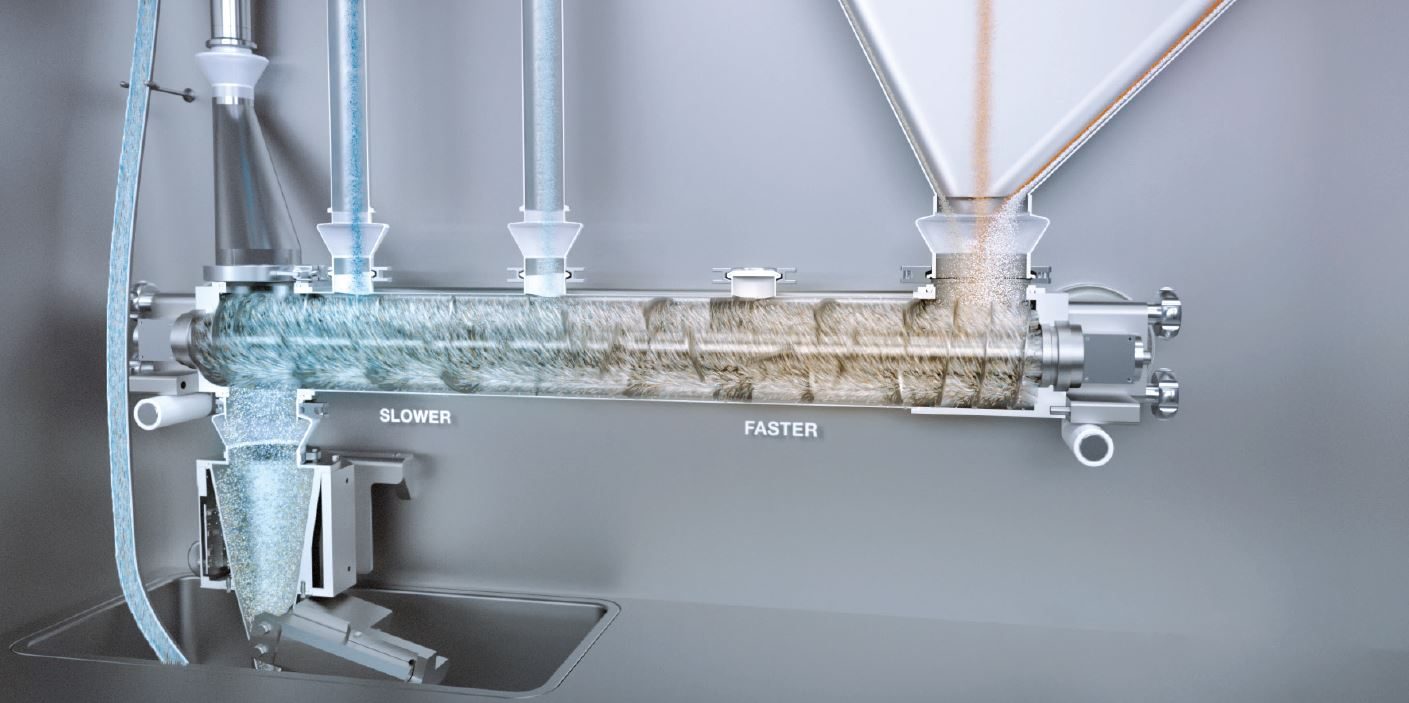
Bild: Fette Compacting
Fördern auf nur einer Raumebene
Auch den letzten Schritt der Tablettierung hat Fette Compacting bei der Entwicklung neu gedacht. Konventionelle Maschinen nutzen in der Regel die Schwerkraft, damit die Pulvermischung zum Einlass der Tablettenpresse gelangt. Damit gehen meist hohe Produktionsräume einher. Für die FE CPS wurde ein spezielles Transportsystem entwickelt, das das Produkt auf nur einer Raumebene per Dichtestromförderung ohne Entmischungsgefahr über eine Strecke von bis zu zehn Metern befördert. Die Mischung gelangt per Förderschlauch flexibel und störungsfrei zum Einlauf der Tablettenpresse. Somit lassen sich die FE CPS und die Tablettenpresse auch in getrennten Räumen aufstellen. Die Installation in einer bestehenden Produktionsanlage kann ohne größere Umbauten erfolgen.
Ein ganzheitlicher Ansatz
Durch die umfassende Betrachtung des Produktionsprozesses ließen sich bei der Entwicklung einzelne Schritte und Technologien zielgerichtet anpassen. Im Ergebnis führte das zu einer kontinuierlichen Direktverpressung mit schlankem Design, hoher Qualität und maximaler Flexibilität. So ist neben der Tablettenverpressung auch die Kapselbefüllung oder eine Trocken- oder Nassgranulation möglich. Bei zahlreichen Produktversuchen mit Kunden zeigte sich sogar, dass sich die Rezepte der Batchherstellung ohne Änderung der Inhaltsstoffe auf der kontinuierlichen Anlage verarbeiten lassen.