Wurden in der Vergangenheit Anlagen in der Chemieindustrie nicht selten für eine Laufzeit von mehreren Jahrzehnten geplant,
so verlangen wachsende Produktvielfalt und starker Kostendruck flexiblere Lösungen. Effizienz und Schnelligkeit zahlen sich hier aus. Doch wie lassen sich diese Herausforderungen meistern und gleichzeitig die hohen Sicherheitsanforderungen an Prozesse und Anlagen in der chemischen Produktion einhalten? Wie können komplexe Anlagen mit einer Vielzahl an Komponenten unterschiedlicher Hersteller schnell angepasst werden? Antworten finden Anlagenplaner und -betreiber in den Richtlinienreihen VDI 2776 zu modularen Anlagen und VDI/VDE/Namur 2658 zur modularen Automation.
Standardisierung der Modulbeschreibung
Für ein durchgängiges modulares Engineering muss es eine herstellerunabhängige Modulbeschreibung geben. Das führte zur Entwicklung des Module Type Package (MTP), das in der VDI/VDE/Namur-2658-Richtlinienreihe standardisiert wird. Es erlaubt die Integration mehrerer Module mit Steuerungen verschiedener Hersteller innerhalb eines übergeordneten Steuerungs- und Managementsystems, dessen Funktionalitäten einem Prozessleitsystem ähnlich sind. Große Teile der Steuerungs- und Regelungsintelligenz werden damit dezentral in die Module verlagert. Über eine einheitliche Schnittstelle kommunizieren die Module mit dem Leitsystem. Erweiterungen oder Umbauten lassen sich so deutlich kostengünstiger und schneller realisieren. Die im Modul integrierte Anlagensicherheit vereinfacht Genehmigungsverfahren und erhöht die Sicherheit der Prozesse auch im Sinne der ökologischen Verantwortung, die Betreiber chemischer Anlagen mehr denn je zu tragen haben. Gerade mittelständische Chemieunternehmen mit ihren relativ kleinen Produktionsmengen gewinnen dadurch Flexibilität und Zuverlässigkeit bei der Planung zukünftiger Prozesse.
CHT wagt Realisierung von MTP in der Produktion
Die CHT Gruppe hat den Schritt in die Umsetzung gewagt. Der Spezialchemikalienhesteller aus Tübingen mit Produktionsstätten auf allen Kontinenten hatte in seinem Stammwerk in Dusslingen schon einige modular gestaltete Prozessanlagen in Betrieb. Nun sollte auch die MTP-Funktionalität im wertschöpfenden produktiven Bereich installiert werden. Ziel war es, nachzuweisen, dass diese neue Technologie im anspruchsvollen Produktionsumfeld wirtschaftlich, flexibel und sicher genutzt werden kann. Günther Schätzle, Manager Plant Engineering Production & Logistics bei CHT, wählte ein bereits implementiertes Verfahren für die Herstellung von Polymeren als Startprojekt am Standort Dußlingen aus. Nach und nach soll das Verfahren auch standortübergreifend durch den Einsatz weiterer modularer Anlagen realisiert werden. Bei der Herstellung von Polymeren kommt es bei der Dosierung der Edukte auf Zuverlässigkeit und Genauigkeit an. Die Produktvielfalt verlangt zudem eine an den jeweiligen Herstellungsprozess angepasste Dosiertechnik. Dafür hat CHT bereits seit vielen Jahren unterschiedliche Typen von mobilen Dosieranlagen im Einsatz, die an die verschiedenen Reaktoren angeschlossen werden. Da sich die Dosieranlagen im Produktionsumfeld bewährt haben, bot es sich für Schätzle an, diese auch für das neue Verfahren zu nutzen. Die Dosierlogik wurde bisher konventionell in das Prozessleitsystem der Reaktionskesselanlagen integriert. Das heißt, jeder Reaktor hielt die notwendigen Programmcodes für den Betrieb der im technischen Detail variierenden Dosiermodule lokal vor und übernahm die Steuerung der mobilen Module, sobald diese angeschlossen wurden.
Nun galt es, die Intelligenz aus den Steuerungen der stationären Reaktoren in das Dosiermodul zu verlagern und anstelle von Schaltpunkten prozesstechnische Dosierdienste anzubieten. Das erforderte die Schaffung einer einheitlichen Schnittstelle unter Verwendung des MTP-Formates, um die Dienste über das Prozessleitsystem abrufen zu können. Die universelle Verwendbarkeit der Dosierdienste im sich verändernden Produktionsumfeld spielte dabei eine wichtige Rolle, denn Produktionsanpassungen bedingen den Einsatz verschiedener Reaktoren und wechselnder Dosiermedien. Zudem waren Überwachungs- und Messeinrichtungen vorzusehen, um die Funktion und Sicherheit zu gewährleisten und dem Bediener Informationen zu erforderlichen händischen Eingriffen zur Verfügung zu stellen.
Wer macht was? Modulares Projekt auf mehrere Unternehmen verteilt
An der Projektrealisierung waren neben CHT ein für die POL (Process Orchestration Layer) zuständiger Systemhersteller und die System- und Komponentenhersteller der modularen Dosiereinheiten, sog. PEA (Process Equipment Assembly), beteiligt. An den Datenschnittstellen haben sie sich auf gemeinsame Spezifikationen für die Industriestandards MTP und OPC UA geeinigt. Für den Dosiervorgang wird das mobile Dosiermodul mit Pumpen und Dosiertechnik von Sera an die jeweilige Produktionsanlage mit Schläuchen angeschlossen und aus IBC-Containern versorgt. Die MTP-Dienste zur Steuerung der Dosierabläufe sowie weitere Sensorik wurden mit der Automatisierungstechnik von B&R integriert. Die Füllstandmessung erfolgt mithilfe von Vega-Geräten und stellt sicher, dass die Anlage im zulässigen Bereich betrieben wird. Der Leckagesensor Spillguard connect von Denios detektiert austretende Flüssigkeiten und löst einen Alarm aus. Die am Dosiermodul gemessenen Sensordaten werden per Mobilfunk auf Basis von Narrowband IoT in die jeweilige Cloudanwendung der Sensorhersteller Denios und Vega übertragen. Semodia stellt mit der MTP Control-Engine eine Software bereit, die beim Start eine aktuelle Geräteliste über die Web-API von Denios und Vega herunterlädt, dynamisch ein MTP-File erzeugt und dieses über einen integrierten Web-Server zum Download bereitstellt. Auf der Leitebene werden die PEA-Module mit dem Kommunikationsstandard OPC UA in das Prozessleitsystem Aprol von B&R integriert.
Echtzeit-Leckageüberwachung mit DIBt-Zulassung
Der kompakt gebaute Leckagesensor Spillguard connect löst bei Leckagen innerhalb des Dosiermoduls einen Alarm aus. Das runde, mit einem Durchmesser von 110 mm einfach zu platzierende System ist mit nur einem Knopfdruck funktionsfähig und überwacht die Auffangwannen rund um die Uhr online. Sollte es zu einer Leckage im Dosiermodul kommen, wird der Alarm in Echtzeit über Narrowband-IoT-Technologie an die cloudbasierten Web-Anwendung für das Leckagemanagement übertragen. Spillguard connect ist für den Umgang mit allen gängigen Gefahrstoffen geeignet und kann auch im Ex-Bereich nach Atex-Zone 0 eingesetzt werden.
Ein weiteres Plus: Der Leckagewarnmelder hat eine DIBt-Zulassung, ein offizielles Zertifikat vom Deutschen Institut für Bautechnik in Berlin. Das bedeutet, er ersetzt die wöchentliche Sichtprüfung der Auffangwannen. Bislang mussten alle Auffangwannen im Betrieb regelmäßig einer Sichtkontrolle unterzogen werden, ob sich darin Flüssigkeiten befinden. Eine Prozedur, die viel Zeit in Anspruch genommen hat. CHT kann sich nun ein Protokoll ausstellen lassen, um für Audits nachzuweisen, dass sämtliche Auffangwannen permanent durch die eingesetzten Spillguard connect überwacht werden. Mittlerweile sind 56 dieser Sensoren im Werk verteilt über MTP eingebunden.
Inbetriebnahme dank MTP innerhalb weniger Minuten
Für den Return on Invest (ROI) rechnet Schätzle nach Abzug der Projektkosten mit einem knapp sechsstelligen Euro-Betrag pro Jahr. Dieser ergibt sich sowohl aus der Aufwandsreduzierung für die Dosiertechnik – Software-Engineering, Andocken (Plug) und Systemsynchronisation (Validate) – als auch aus der Material- und Aufwandsreduzierung für das Leckagemanagement. Durch die schnelle Kopplung des Dosiermoduls an das Prozessleitsystem unter Verwendung des MTP-Formats und einer OPC-UA-Schnittstelle reduzieren sich die Zeiten für die Inbetriebnahme bis auf wenige Minuten. Die Überwachung der Anlage konnte aufgrund der mobilen, cloudbasierten Datenübertragung ohne großen Verkabelungs- und Elektroinstallationsaufwand sichergestellt werden. Der in der Dosier-PEA integrierte Dosierservice lässt sich aufgrund des hohen Standardisierungsgrads problemlos als Plug- & Play-Lösung auch für andere Dosieraufgaben in der Verfahrenstechnik verwenden.
Denios GmbH, Bad Oeynhausen
CHT Germany GmbH, Tübingen
Daniela Held
Redakteurin
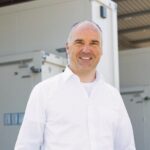
Nachgefragt: Mit MTP raus aus der Testphase
Was gab für CHT den Anstoß, MTP in der Produktion einzusetzen?
Günter Schätzle: Wir bei CHT sind schon immer mutig gewesen, wenn es um neue Technologien geht. CHT hat sich bereits vor zehn Jahren mit der Modularisierung von Produktionsanlagen beschäftigt und solche Anlagen gebaut. Bislang wurden MTP-Projekte nur im Labor und Technikumsbereich umgesetzt. Im Jahr 2021 haben wir beschlossen, ein System für den Produktionsbereich aufzubauen, das alle Anforderungen an den modularen Apparatebau erfüllt. Dafür haben wir eine Dosieranlage wie sie schon in Betrieb ist umgebaut, um eine Datenübertragung per MTP zu ermöglichen. Bisher wurden die mobilen Dosierstationen über Datenkabel an das Prozessleitsystem der Reaktionskesselanlagen angeschlossen und von dort wurde die Dosiersteuerung übernommen.
Welchen Vorteil versprechen Sie sich nun von MTP?
Schätzle: Wir haben sehr viele kleine Produktionsstätten auf der Welt, müssen schnell auf Marktänderungen reagieren können. Wir wollen Anlagen nicht mehr über Jahrzente betreiben, sondern einen Fuhrpark aus Produktionskomponenten schaffen, die miteinander kombinierbar sind und einfach in die zentrale Steuerung eingebunden werden können, also echtes Plug & Produce.
Wie sieht das im konkreten Fall der Dosieranlage aus?
Schätzle: Wir haben jetzt eine autarke Dosieranlage mit lokaler Intelligenz, die über das Datenformat MTP mit dem Prozessleitsystem kommuniziert. Die Dosieranlage kann völlig autark betrieben werden. Wird sie an einer Apparatur eingesetzt, führt sie den Dienst „Dosieren“ aus. Auf der Modulebene befindet sich ein OPC-UA-Server und das PLS ist OPC-UA-Client. Das MTP-File beschreibt, was auf dem Server zu finden ist und welcher semantische Hintergrund vorliegt, z. B. Füllstand in 0 bis 100 %. Diese Information kann vom Leitsystem eingelesen werden.
Wie beurteilen Sie die Zusammenarbeit mit den Projektpartnern?
Schätzle: Im Laufe des Projekts hat uns das Engagement aller Projektbeteiligten begeistert. Es herrschte Goldgräberstimmung, die hoffentlich Initialwirkung hat. Je mehr Anwender diese Lösung adaptieren, desto günstiger wird sie. Die Standards zur Modularisierung und Vernetzung der Produktionsabläufe müssen sich nur noch deutlich stärker in der Praxis durchsetzen. Die CHT Gruppe verfolgt diese Ansätze seit Langem und gestaltet den Richtlinienprozess aktiv mit.
Wie wirkt sich der Einsatz der MTP-Technologie kostenseitig aus?
Schätzle: Der ROI hat sich nach fast einjähriger Betriebserfahrung mit der neuen Technologie bewahrheitet. Wir konnten mit unserem Projekt nachweisen, dass die verfahrenstechnische Normierung für den Bau modularer Chemieanlagen nach VDI 2776 für die Anwendung in wertschöpfenden Prozessen einsetzbar ist. Und wir haben gezeigt, dass es möglich ist, MTP produktiv zu nutzen. Unser Ziel ist es, am Ende von den Zulieferern Module kaufen zu können, die man einfach zusammenstecken kann wie früher die Stereoanlage. Auf diese Weise kann man Kosten sparen. Wir werden nun bei jeder Anlage prüfen, ob das MTP-Konzept sinnvoll ist.